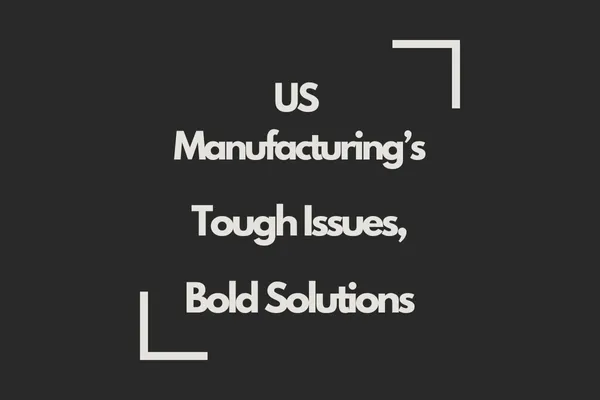
Digital Twin vs Digital Mirage
Digital Twin vs. Digital Mirage: Avoiding Common Pitfalls in Your First Implementation
"We thought we were building a digital twin. Turns out, we were just building a prettier dashboard."
Those were the exact words from Raj, co-owner of a 50-person industrial equipment manufacturer in Illinois. He and his team invested in sensors, data integration, and a flashy software platform promising real-time insights. But months later, they had no actionable insights, growing frustration, and a stack of consultant invoices.
What went wrong?
It’s a story that’s becoming all too common among small and mid-sized manufacturers (SMEs): chasing digital transformation, investing in the hype, and ending up with a “digital mirage” — a system that looks good on the surface but offers little operational value.
Digital twins can absolutely transform a manufacturing operation. They can reduce downtime, optimize processes, improve collaboration, and even drive sales. But like any powerful tool, they need to be implemented with the right goals, expectations, and structure — otherwise, they risk becoming expensive tech experiments with little return.
In this article, we’ll break down:
What a real digital twin is (and what it’s not)
The most common mistakes SMEs make
How to avoid wasted time, money, and confusion
Real-life lessons from SMEs who got it right — and wrong
What a Digital Twin Really Is — and What It’s Not
Let’s start by clearing the air.
A digital twin is a virtual, dynamic model of a physical asset, system, or process that is continuously updated with real-time data. It doesn't just display information — it simulates, predicts, and informs decisions. It’s about behavior, not just appearance.
A Real Digital Twin:
Mirrors the state and behavior of a machine or process in real-time
Is connected to live operational data (via IoT, PLCs, MES, etc.)
Enables simulation, prediction, and optimization
Integrates with business systems (ERP, scheduling, maintenance)
A Digital Mirage:
Is just a 3D model or CAD file
Lacks real-time or actionable data
Is siloed from operational or business systems
Looks great in demos but doesn’t inform decisions
This misunderstanding is the root of many failed implementations.
Common Pitfalls in Digital Twin Projects (and How to Avoid Them)
Pitfall 1: Starting with a Grand Vision Instead of a Practical Problem
Many SMEs try to launch digital twins across their entire operation — every machine, every process, every department. The result? Scope creep, delays, and ballooning costs.
Fix: Start Small and Specific
Identify a single, high-impact use case — like predicting failure in your most critical machine, or simulating layout changes on your bottleneck line. Build a pilot, prove ROI, then scale.
Example: A fabrication shop in Pennsylvania started with a digital twin for just one robotic welder. They detected a recurring nozzle clog issue and reduced unplanned downtime by 20% in three months — before rolling it out to the rest of the cell.
Pitfall 2: Thinking 3D Visualization = Digital Twin
It’s easy to get wowed by interactive models and dashboards. But if those visuals aren’t connected to live data, they're just digital "posters" — not living twins.
Fix: Connect to Real Data Early
Make sure your model pulls live operational data (temperature, RPMs, status, etc.). Even a simple, text-based digital twin with sensor inputs can be more useful than an impressive 3D mockup with no context.
Stat to know: According to Gartner, over 60% of early-stage digital twin projects fail to move past the visualization phase — offering little value beyond aesthetics.
Pitfall 3: Ignoring the Human Factor
A powerful digital twin is worthless if your team doesn’t use it. If operators don’t trust the data, or managers see it as a burden, it will quietly die on the shop floor.
Fix: Involve Users from Day One
Include operators, maintenance techs, and production leads in the design and rollout. Build interfaces that speak their language and improve their day-to-day work — not just check a “digital transformation” box.
Example: One SME in the plastics industry built a temperature monitoring twin. It flopped — until they added color-coded alerts and mobile notifications for line leads. Adoption skyrocketed, and process stability improved.
Pitfall 4: Not Planning for Integration
Many SMEs get stuck with digital twins that can’t talk to their ERP, MES, or maintenance systems — forcing redundant work and breaking the data chain.
Fix: Design with Integration in Mind
Choose platforms that play well with your existing systems — or that offer APIs and plug-ins for future expansion. Interoperability is key.
Recommended Tools:
PTC ThingWorx – Good for integrating IoT data with MES/ERP
Microsoft Azure Digital Twins – Strong ecosystem for SMEs already using Office 365 or Dynamics
Tulip Interfaces – Low-code with pre-built integrations for SME environments
Real-Life Lessons: The Good, the Bad, and the Valuable
Success Story: Lean Win with a Digital Twin Pilot
A small packaging manufacturer in North Carolina started with a digital twin of their bagging line. They added a few sensors, connected data to a dashboard via MindSphere, and simulated various staffing patterns.
Result? They discovered that staggered shift starts reduced micro-stoppages and increased throughput by 12% — without adding any new equipment.
Cost of implementation: ~$8,000
ROI: Achieved in 3 months
Failure Story: Fancy Model, No Results
A CNC shop in Arizona hired a consultant to build a full-factory digital twin using custom Unity visualizations. The model was impressive — but required manual data entry, lacked predictive capability, and couldn’t interface with the shop’s ERP.
After six months and $30,000, the tool was abandoned.
Lesson? Function beats form. Always.
Checklist: How to Avoid the Mirage and Build the Right Twin
Define a measurable problem to solve
Start with one machine or process
Connect real-time data feeds early
Keep visuals simple, focus on insight
Involve the people who’ll use it
Plan for system integration
Track ROI metrics (downtime, scrap, cycle time)
Scale only after the pilot proves value
Conclusion: A Digital Twin is a Tool, Not a Trophy
Digital twins can be powerful. But they’re not magic, and they’re certainly not one-size-fits-all. For small and medium-sized manufacturers, success doesn’t come from chasing the most high-tech solution — it comes from solving real problems with smart, scalable tools.
Your first digital twin doesn’t need to be perfect. It just needs to be useful. Start small, stay focused, and remember — the goal isn’t to build something flashy. The goal is to build something that makes your business run better.
References & Further Reading
Gartner – Digital Twin Hype Cycle Report 2023
McKinsey & Company – How to Ensure Digital Manufacturing Delivers Value
Siemens MindSphere – Real-time industrial IoT platform
Microsoft Azure Digital Twins – Build, model, and track smart spaces
PTC ThingWorx – Industrial IoT and digital twin for SMEs
Curious About Digital Twins or Digital Transformation — But Not Sure Where to Start?
You don’t have to figure it out alone. At Strategic Value+ Solutions, we specialize in helping small and mid-sized manufacturers take the right first step into Industry 4.0 — with real-world strategies, not tech jargon.
Whether you're looking to reduce downtime, improve efficiency, connect your departments for coordinated decision-making, or explore digital twin technology, our veteran experts will help you uncover opportunities and avoid common pitfalls.
Let’s make digital transformation work for you — simply, strategically, and successfully.
To give you a heads-up about how to introduce digital twin advantages to your manufacturing company, we have developed a simple, actionable Digital Twin Pilot Checklist specifically for small and medium-sized manufacturers (SMEs). This checklist will help you learn how to plan, execute, and evaluate your first digital twin implementation without overcomplicating it.
COMPLETE THE FORM TO DOWNLOAD THE FREE GUIDE NOW
Exclusive Offer: We’re offering a complimentary 45-minute discovery session to help U.S. manufacturers assess the pros & cons of AI, automation, and digital twin adoption -- no pressure, just practical insights tailored to your business. Let’s strategize your path forward!
CLICK HERE TO SCHEDULE A FOCUSED CONVERSATION about your manufacturing company and get your AI, automation, and digital twin questions answered.
Have questions? Text Roy at +1 919-589-3580 or email Nel at [email protected] .
#DigitalTwinImplementation
#DigitalTransformation
#TechStrategy
#SMBManufacturing
#AvoidTechFailures
#Industry40Challenges
#DigitalSuccess
#SmartFactoryStrategy
#IIoTInsights
#FutureOfManufacturing
[This article is also published in the U.S. Manufacturing Newsletter on LinkedIn]