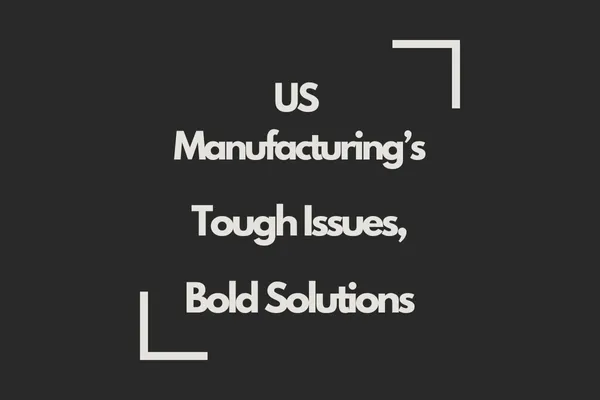
Digital Twins on a Budget: How SMEs Can Compete with Enterprise Giants
“We thought digital twins were only for the GEs and Siemens of the world.”
That’s what Alan, the owner of a mid-sized injection molding company in Ohio, said when he first heard the term "digital twin." Like many small and medium-sized manufacturers (SMEs), Alan assumed digital twins were just another buzzword — too expensive, too complex, and best left to companies with million-dollar tech budgets and in-house engineering teams.
But today, Alan’s factory floor runs smoother than ever. His machines notify him before they break down. He can simulate new product designs virtually, and he even landed a big contract by showcasing a digital prototype instead of investing in physical tooling. All this thanks to a digital twin system that cost less than a new forklift.
So what changed? And how can other SME owners like Alan get started?
What is a Digital Twin, Really?
At its core, a digital twin is a virtual replica of a physical asset, process, or system. It collects real-time data via sensors, IoT devices, and software integrations to reflect how the asset performs — and even predict how it will perform.
In manufacturing, this could mean:
A machine-level digital twin monitoring vibration, temperature, and output to predict failure.
A process-level twin simulating your production line for bottlenecks.
A product-level twin letting customers visualize and test configurations in real time.
Large manufacturers have been using digital twins for years. But today, costs are dropping, platforms are becoming more accessible, and even plug-and-play solutions are available — making it viable for SMEs.
Why Should SMEs Care?
Let’s face it — downtime, waste, and inefficiency hurt small manufacturers more than anyone. You can’t afford to waste a production day due to a machine breakdown or lose a client due to slow prototyping.
Here’s how digital twins give SMEs a competitive edge:
1. Cut Downtime with Predictive Maintenance
According to Deloitte, unplanned downtime costs manufacturers an estimated $50 billion annually, and equipment failure is the leading cause. With digital twins, you can monitor the health of your machinery in real time. Instead of reacting to breakdowns, you anticipate them.
Example: A small metal stamping company used a digital twin to monitor hydraulic press performance. When a pressure anomaly popped up, they preemptively replaced a valve — avoiding a 3-day shutdown that would’ve cost them $30,000 in lost production.
2. Accelerate Design and Prototyping
Instead of building costly physical prototypes, SMEs can simulate designs digitally, get customer feedback faster, and make changes before committing to materials or tooling.
Example: A mid-sized electronics manufacturer used Siemens’ Solid Edge software (which includes digital twin capabilities) to create virtual prototypes of enclosures. Their time-to-quote dropped by 35%, helping them win more business.
3. Improve Process Efficiency
Digital twins can help visualize your shop floor, simulate production schedules, or optimize workflows. This is especially useful for batch manufacturing and custom orders.
Stat to know: According to PwC, manufacturers that use digital twins see up to a 25% improvement in operational efficiency.
But Isn’t It Expensive?
Here’s the good news: not anymore.
Thanks to cloud computing, open-source platforms, and pay-as-you-grow models, SMEs can dip their toes in without breaking the bank.
Budget-Friendly Digital Twin Tools:
PTC ThingWorx – Offers scalable IoT/digital twin functionality. Great for SMEs focused on machine monitoring.
Siemens Solid Edge with Xcelerator – Affordable CAD with digital twin features, tailored for smaller manufacturers.
Azure Digital Twins – Microsoft’s platform is free to start with, and you pay as you scale. Ideal if you're already using Microsoft 365 or Azure.
TwinCAT from Beckhoff – Good for real-time control and automation systems, often used in compact factories.
Some companies start by creating a digital twin of just one machine — a CNC router, an extruder, or a packaging line — and grow from there.
Getting Started: A Step-by-Step Playbook
Identify a High-Impact Use Case Don’t start with your entire factory. Start small. What’s your biggest pain point? A frequently failing machine? A slow prototyping process?
Gather Your Data Many SMEs already have data — it’s just sitting in PLCs, spreadsheets, or legacy systems. Connect your machines via inexpensive IoT gateways.
Choose the Right Tools Select a platform that integrates with your existing tech stack. Look for low-code or no-code platforms if you don’t have in-house developers.
Pilot and Learn Build a simple twin of one asset or process. Run it for a few weeks. Track metrics like downtime, scrap rate, or production speed.
Scale Strategically Once you see results, expand. Create twins of your entire production line, simulate scheduling, or even use AI to optimize layouts.
The Payoff: Punching Above Your Weight
Digital twins used to be the domain of aerospace giants and smart factories with bottomless R&D budgets. But not anymore. SMEs like yours can use them to:
Compete on speed and customization
Reduce costly downtime
Win clients with faster iterations
Make smarter capital investments
In a world where manufacturing is getting leaner, faster, and more digital — digital twins are your ticket to staying competitive without going broke.
And just like Alan discovered, it’s not about having the biggest budget — it’s about being the smartest and most agile player in the game.
References & Further Reading:
Deloitte. The economic impact of unplanned downtime.
PwC. Digital Factories 2020: Shaping the future of manufacturing.
Siemens. Solid Edge for small and medium businesses.
Microsoft Azure Digital Twins.
PTC ThingWorx.
Curious About Digital Twins or Digital Transformation — But Not Sure Where to Start?
You don’t have to figure it out alone. At Strategic Value+ Solutions, we specialize in helping small and mid-sized manufacturers take the right first step into Industry 4.0 — with real-world strategies, not tech jargon.
Whether you're looking to reduce downtime, improve efficiency, connect your departments for coordinated decision-making, or explore digital twin technology, our veteran experts will help you uncover opportunities and avoid common pitfalls.
Book your FREE 45-minute strategy session today — no pressure, just practical insights tailored to your business.
Let’s make digital transformation work for you — simply, strategically, and successfully.
#DigitalTwin
#SmartManufacturing
#Industry40
#ManufacturingInnovation
#SMEtech
#DigitalTransformation
#LeanManufacturing
#IoTforSMEs
#FactoryOfTheFuture