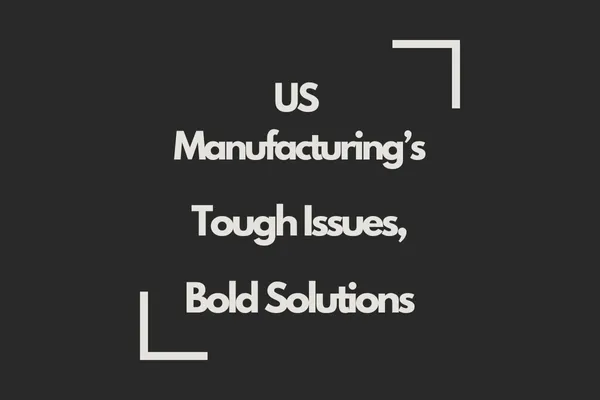
The Workforce Crisis: Bridging the Skills Gap in U.S. Manufacturing
“The National Association of Manufacturers (NAM) reports that 82% of executives say the inability to find skilled talent directly impacts their ability to meet customer demand, delaying production and stifling innovation.” - National Association of Manufacturers
Introduction
The U.S. manufacturing sector is at a pivotal moment in its history. Once the bedrock of American economic prosperity, the industry is now grappling with a workforce crisis that could hinder its ability to compete in the global market. The skills gap—defined as the disconnect between the skills employers need and the qualifications of the available workforce—has reached a critical stage, directly affecting productivity, innovation, and growth. Addressing this challenge requires deeper critical thinking, innovative approaches, and a unified commitment from businesses, educators, and policymakers.
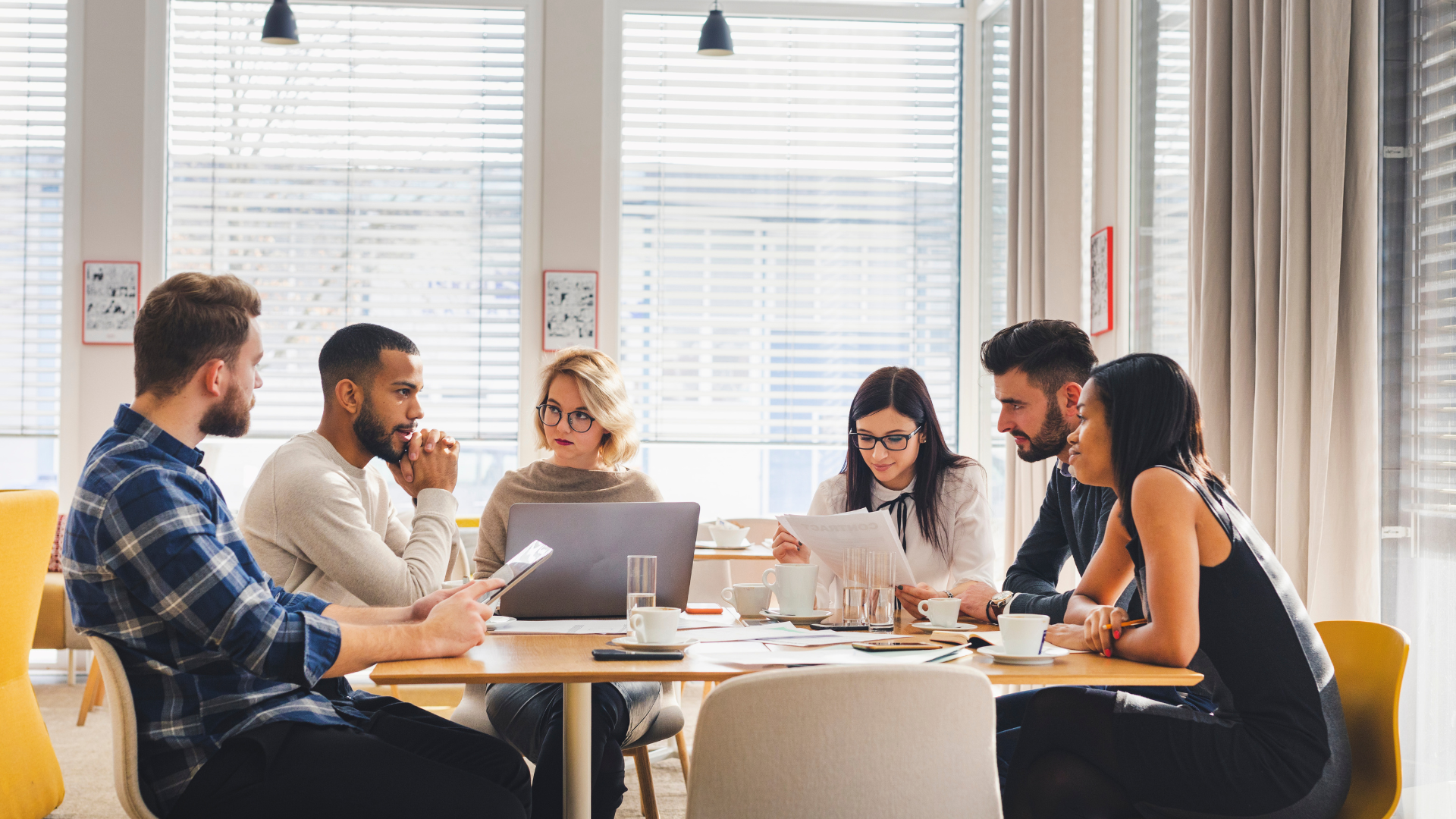
Understanding the Skills Gap: More Than a Numbers Game
The Complexity Behind the Problem
The skills gap is not just a statistical anomaly—it reflects systemic challenges that have evolved over decades. The convergence of automation, artificial intelligence, and digital transformation has revolutionized manufacturing processes, demanding a workforce proficient in advanced technical skills. However, the U.S. education system has been slow to adapt, often prioritizing traditional academic pathways over vocational and technical training. Moreover, as the baby boomer generation retires, the manufacturing sector is losing not just workers but decades of institutional knowledge and experience.
This issue is further exacerbated by public perception. Many young Americans still associate manufacturing with outdated, labor-intensive work environments, rather than the high-tech, innovative spaces they have become. Without addressing this misperception, efforts to attract a new generation of talent will face significant hurdles.
________________________________________
The Current Scope: Alarming Statistics and Economic Implications
By the Numbers
The skills gap is no longer a looming threat—it is an ongoing crisis. Consider these alarming statistics:
• 2.1 million jobs could go unfilled by 2030, according to a 2021 Deloitte and Manufacturing Institute study. This could result in $1 trillion in lost economic output annually.
• The National Association of Manufacturers (NAM) reports that 82% of executives say the inability to find skilled talent directly impacts their ability to meet customer demand, delaying production and stifling innovation.
• The average manufacturing job vacancy lasts 70 days, compared to the 48-day national average across all industries, reflecting the difficulty of finding qualified candidates.
These numbers illustrate the urgency of the problem but also highlight the opportunities for manufacturers that can overcome these challenges.
________________________________________
Real-World Examples: Lessons from the Field
Boeing: Building Talent Pipelines
Boeing, one of the world’s leading aerospace manufacturers, has faced acute challenges in recruiting machinists, engineers, and technicians. Recognizing the need for a proactive solution, Boeing launched partnerships with local community colleges to offer specialized training programs. For instance, its collaboration with St. Louis Community College provides students with hands-on experience in aerospace manufacturing, preparing them for well-paying jobs within the company.
Caterpillar: Upskilling as a Strategy
Caterpillar, a global leader in heavy equipment, understands the necessity of upskilling its workforce. Through initiatives like the "ThinkBIG" program, Caterpillar trains technicians in advanced equipment diagnostics and maintenance. The program combines classroom instruction with real-world experience, ensuring that graduates are immediately productive.
SMEs: The Struggle to Compete
Small and mid-sized manufacturers (SMEs) often lack the resources to develop comprehensive training programs. For example, a family-owned metal fabrication company in Ohio found itself losing contracts due to a shortage of skilled welders. Unable to compete with larger corporations offering higher salaries, the company partnered with a nearby vocational school to create a custom welding apprenticeship program. This approach allowed them to address their specific workforce needs while building a sustainable talent pipeline.
________________________________________
Blueprint for Bridging the Gap
Addressing the skills gap requires a strategic, multi-pronged approach. Below is a step-by-step blueprint that manufacturers can follow to begin making practical, measurable progress:
Step 1: Conduct a Workforce Audit
• Objective: Identify the specific skills gaps within your organization.
• Action Plan: Evaluate current employee competencies against the technical and soft skills required for future growth. Use tools like skill assessments, interviews, and external consultants to create a detailed gap analysis.
Step 2: Forge Partnerships with Educational Institutions
• Objective: Align educational curricula with industry needs.
• Action Plan: Collaborate with community colleges, vocational schools, and universities to co-develop training programs. For example, Siemens has partnered with high schools to offer dual-enrollment programs, combining academic study with technical training.
Step 3: Develop Apprenticeship and Internship Programs
• Objective: Provide hands-on learning opportunities for students and early-career workers.
• Action Plan: Create paid apprenticeships and internships that blend classroom instruction with on-the-job training. Offer clear pathways for participants to transition into full-time roles.
Step 4: Invest in Continuous Upskilling
• Objective: Ensure that current employees remain competitive in an evolving industry.
• Action Plan: Introduce regular training sessions, workshops, and digital learning platforms to teach new skills. Companies like Amazon have embraced online courses to reskill warehouse workers for technical roles.
Step 5: Modernize Talent Acquisition Strategies
• Objective: Attract younger, tech-savvy talent to the manufacturing industry.
• Action Plan: Launch targeted marketing campaigns to highlight the high-tech nature of modern manufacturing. Showcase employee success stories and emphasize career advancement opportunities.
Step 6: Advocate for Policy Support
• Objective: Secure government funding and incentives for workforce development.
• Action Plan: Engage with local and national policymakers to push for increased investment in vocational education, tax credits for training programs, and public-private partnerships.
________________________________________
Long-Term Implications and Call to Action
The skills gap in U.S. manufacturing is a multifaceted challenge, but it is not insurmountable. Addressing it requires a concerted effort across industries, education, and government. By investing in the workforce of the future, manufacturers can not only solve their immediate talent shortages but also position themselves for sustained growth and innovation.
For Business Leaders
• Embrace workforce development as a core business strategy.
• Prioritize partnerships and investments that create long-term talent pipelines.
For Educators
• Redesign curricula to align with industry demands.
• Work with businesses to provide hands-on learning opportunities.
For Policymakers
• Increase funding for STEM and vocational programs.
• Provide tax incentives for companies investing in workforce training.
________________________________________
Conclusion
The workforce crisis in U.S. manufacturing is a defining challenge of our time. Bridging the skills gap is not just an economic necessity but a strategic opportunity to reimagine the industry. Through collaboration, innovation, and a commitment to workforce development, American manufacturing can maintain its global leadership and secure a prosperous future for generations to come.
________________________________________
References
1. Deloitte and Manufacturing Institute. (2021). The Skills Gap in U.S. Manufacturing: A 2030 Outlook.
2. National Association of Manufacturers. (2023). Workforce Development Initiatives in Manufacturing.
3. U.S. Bureau of Labor Statistics. (2023). Occupational Outlook Handbook.
4. Siemens USA. (2022). Creating Tomorrow’s Workforce: Dual Enrollment Programs.
5. Amazon. (2021). Upskilling 2025: Investing in Workforce Training.
6. Manufacturing Institute. (2023). State of the Workforce Report.
________________________________________
Resources
Resources for Further Research on Bridging the Skills Gap in Manufacturing
Here is a curated list of resources to deepen your understanding of the workforce crisis in U.S. manufacturing and explore solutions for bridging the skills gap:
________________________________________
Reports and Studies
1. Deloitte and The Manufacturing Institute: The Skills Gap in U.S. Manufacturing 2021 Report
Read the report for data-driven insights into the workforce challenges facing U.S. manufacturing and projections through 2030.
2. National Association of Manufacturers (NAM): Manufacturing Workforce Development Playbook
A practical guide offering strategies for addressing workforce challenges and case studies from leading manufacturers. Visit NAM’s website.
3. The Manufacturing Institute: State of Manufacturing Reports
Annual reports that highlight workforce trends, challenges, and success stories in manufacturing. Available at The Manufacturing Institute.
4. McKinsey & Company: The Future of Work in Manufacturing
Analysis on how technology and automation are reshaping the workforce landscape. Access the study at McKinsey’s website.
________________________________________
Government and Policy Resources
5. U.S. Department of Labor: Registered Apprenticeship Program (RAP)
Information on creating and expanding apprenticeship programs tailored to manufacturing. Visit DOL RAP.
6. National Science Foundation (NSF): Advanced Technological Education Program
Funding and resources to support workforce education in manufacturing technologies. Learn more at NSF ATE.
7. SkillsUSA: A nonprofit organization dedicated to improving technical and vocational education. Provides competitions, training, and resources for manufacturing career paths. Visit SkillsUSA.
________________________________________
Education and Training Resources
8. Association for Career and Technical Education (ACTE): Resources for STEM and CTE Education
Offers tools and best practices for aligning educational programs with industry needs. Explore resources at ACTE.
9. Tooling U-SME: Online Manufacturing Training Programs
A leader in workforce development, providing online courses tailored to manufacturing skills. Visit Tooling U-SME.
10. Community College Research Center (CCRC): Research on the role of community colleges in workforce training and industry partnerships. Visit CCRC.
________________________________________
Professional Associations and Networks
11. Society of Manufacturing Engineers (SME): Offers certifications, training, and networking opportunities for professionals in manufacturing. Visit SME.
12. American Welding Society (AWS): Resources for welding education, certification, and training programs. Visit AWS.
13. National Skills Coalition (NSC): Advocacy and research organization focused on workforce development policies. Visit NSC.
________________________________________
Case Studies and Success Stories
14. Siemens USA Workforce Development: Learn about Siemens’ dual-enrollment programs and apprenticeship initiatives. Visit Siemens USA.
15. Amazon Upskilling 2025 Initiative: A comprehensive approach to workforce training in technical roles. Read more at Amazon Careers.
16. Boeing Workforce Development Programs: Information on Boeing’s partnerships with community colleges and training initiatives. Visit Boeing.
________________________________________
Technology and Innovation in Manufacturing
17. Advanced Robotics for Manufacturing (ARM) Institute: Focused on advancing robotics and workforce education in manufacturing. Visit ARM Institute.
18. National Institute of Standards and Technology (NIST): Manufacturing Extension Partnership (MEP)
Programs and resources for small and mid-sized manufacturers. Visit NIST MEP.
19. Robotics Education & Competition Foundation (REC Foundation): Promotes STEM education through robotics competitions and training programs. Visit REC Foundation.
________________________________________
Articles and Blogs
20. Harvard Business Review (HBR): Articles on workforce trends and strategies for closing skills gaps. Access HBR articles at HBR.org.
21. IndustryWeek: Regular features on workforce development, manufacturing trends, and technology adoption. Visit IndustryWeek.
22. Forbes Manufacturing Insights: Analysis and opinion pieces on the future of the manufacturing workforce. Visit Forbes Manufacturing.
_______________________________________
Advisors: Strategic Value+ Solutions
The Strategic Value+ Solutions Advisors are dedicated to synergistically creating and leveraging U.S. Manufacturing competitive advantages and promoting best practices for enduring profitability and international leadership.
We can help you acquire ISO 9001 certification, and work with you to achieve other valuable certifications.
Schedule a complimentary 90-minute 360-Degree Discovery Session with our Experts. The goal of the session is to help U.S. Manufacturing companies uncover compromising blind spots and lend a fresh eye on opportunities for increasing business value and profitability.
Schedule a session between your U.S. Manufacturing company's leadership team and our veteran advisory team:
Brian McCollough - MBA, CEPA®, CMAA® - Executive Consulting, EOS, Operations & Supply Chain Optimization, Strategic Business Planning, Contract Negotiation, Executive Transition Planning, M&A, KPIs
Ruoyu Loughry - CPA, Executive Consulting, Finance and Accounting, Management and GAAP Financial Reporting, International Business Strategies, KPIs
Roy Dickan - Executive Consulting, AI, Business, Marketing, Sales, Lead Generation, and Operations Automations
Steven Shrinsky - Executive Consulting, Human Resources Management & Compliance, Workforce Analysis/Recruiting/Retention/Training/Development/Safety, Employee Handbooks, OSHA Compliance
Nelinia (Nel) Varenas, MBA - Executive Consulting, Business & Marketing Strategy and Systems Implementation, Internal and External Communications, Brand Strengthening and Management, Company Culture, Public Relations
Maria L. Perez - EdM, CAS, TLCE, Executive Consulting, Creating Meaningful Campaigns for Purpose-Driven Organizations to Amplify Their Impact, Stand Out, & Align with Their Cause, Cause Marketing & Strategic Sponsor Partner Acquisition Expert
Jessy Lee - Mechanical Engineer, Executive Consulting, International Business, Advancing Companies and Increasing their Global Footprints for Optimized Growth, Bridging Gaps in Businesses, Technologies and Cultures.
Mike Liu - PhD, Materials Science & Engineering, Executive Consulting, Co-Founder and CEO of the FreeFuse Multipath Media platform
NOTE: This article is also published in our LinkedIn U.S. Manufacturer Newsletter.
usmanufacturingtalentrecruitment #usmanufacturing #talentrecruitment #usmanufacturingbranding #usmanufacturingimage #digitaltransformation #manufacturingai #manufacturingmisconceptions #manufacturingmythss